プロセス制御が行われたハードターニングセルは、18 日間で元が取れたといいます。
Equator プログラマブルゲージを使用すると、ベアリングの加工およびパーツの分類のための究極の自動生産セルを形成できます
米国テキサス州コンロー – Conroe Machine では、自動制御プロセスで稼動する無人セルにより 24 時間体制でパーツのハードターニングを行うという、多くの加工工場が理想とする製造体制を整えています。ここでは、Fanuc ロボットに Equator ゲージングシステムを統合しており、ツインスピンドルのオークマ 2SP-250 旋盤の全品検査と自動補正のために、レニショーの EZ-IO ソフトウェアを使用して包括的でシンプルな通信機能を確保しています。このセルでは、完成パーツの箱詰めとパレットへの積載も行っています。同社は、このターニングセルに対する投資も 18 日間という驚異的な早さで元が取れたといいます。
Conroe は、今日の若手自動化エキスパートの才能の活用に意欲的な工場が、レニショーの Equator プログラマブルゲージのような新しい技術を活用できることを示すいい例です。同社では、CNC プログラマー、James Wardell 氏とロボット工学技術者、Jeff Buck 氏がソフトウェア開発とプログラミングを行っています。さらに、同社の自動化チームは 2 台の Equator、FANUC ロボット、ビジョンシステム、複数レーンの低プロファイルコンベヤを組み込んだ、顧客向けの無人化パーツ測定/ソーティングセルの作成に取り組んでいます。いずれのアプリケーションでも、Equator が一連のベアリングレースをコスト効果に優れた手段で素早く測定して、プログラム可能な比較検査の真価を発揮しています。ここでは、治具を使用する必要がなく、加工現場環境による問題もありません。
Conroe Machine は、Murray Touchette 氏(通称「Tippy」)が、利用できる中で最高の製造技術を使用してパーツを製造することを目標にして、2000 年に設立した比較的新しい企業です。同社は急速に拡大しており、現在では温度調整された面積 6 千平方メートルの工場で 150 人の従業員が働いています。Conroe は汎用的な工場ですが、ヒューストンに近いという立地から、ほとんどが石油・ガス産業からの取引が多く、ボーリング用のコンポーネントが主体になっています。同社がこの分野で継続的に実施している業務の一つに、ダウンホールマッドモーター用のスラストベアリングレースの製造があります。この一環で、24 時間体制により、毎週数千個のパーツを製造しています。
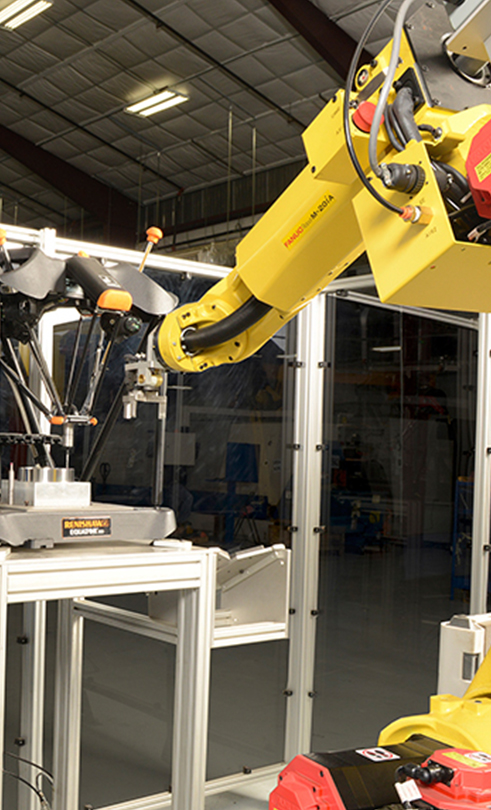
自動化の推進
現在ベアリングの荒加工に使用されている 4 台の Doosan Puma 旋盤は、当初荒加工と仕上げ加工に使用していたもので、運転には 4 人の作業者が必要でした。現在は、これらの機械を 2 つのセルに分け、FANUC ロボットによりロードとアンロードを行って荒加工のみに使用しています。これらのセルは、同社の初期の自動化プロジェクトで自動化を行いました。ここで半仕上げされたパーツを 1.7mm の深度でHRC65のケースハードニングを行ってから、仕上げ加工を行います。
「これら 2 つのセルの生産量は、一日 800 ~ 1000 パーツで頭打ちになっていました。つまりセルあたり 400 ~ 500 パーツです。」と James Wardell 氏は説明します。「1 人の作業者が機械へのロードとパーツの検査を担当していましたが、作業者が正確に検査できるパーツの数には限界があり、生産量を増加する必要がありました。」
Equator を選んだ理由
「次のステップとして、自動パーツローディング、ポストプロセス測定、自動工具補正、パーツ彫刻、パーツの箱詰め/パレット積載を行う完全自動の仕上げ加工プロセスを構想しました。」と James Wardell 氏は続けて説明します。「このようなシステムのコンポーネントについては、かなりよく認識していましたが、パーツ測定テクノロジー、CNC タイプ、工具補正用のソフトウェアは把握していませんでした。最短 98 秒というパーツのサイクル時間に対応するためには、検査も高速で行う必要があります。当初は、そのスピードのために白色光レーザー検査を検討しましたが、パーツの反射度が高すぎました。その後、ハードゲージングと現場用 CMM も検討しました。ハードゲージングは費用が高すぎ、セットアップにも注意が必要になります。一方、CMM はスピードが欠如していました。しかし、他のプロジェクトでレニショーと話しているときに、地域マネジャーの Sheila Schermerhorn に可能性のあるソリューションとして Equator を紹介してもらいました。」
当社の加工セルには、Equator に匹敵するコスト効果を備えた現場測定ツールは他にありません。
Conroe Machine (米国)
プロセス制御ツールとソフトウェア
Equator はゲージング専用機の代わりに使用できる低コストの柔軟なシステムで、比較測定方式を採用しています。Equator では、CMM で寸法を測定したマスターパーツに対して、その後の測定値を比較します。繰返し精度は、マスタリング直後から 0.002mm が得られます。Equator は、現場の温度変化を補正するためにいつでもリマスタリングを行うことができます。Equator は、SP25 プローブを使用して、毎秒最高 1000 データポイントの速度でタッチデータとスキャニングデータを収集します。スタイラスは、統合された 6 ポートのスタイラスオートチェンジラックに格納され、システムのプログラミングには、MODUS™ Equator ソフトウェアを使用します。Equator は押しボタンを使用して簡単に手動操作できますが、Conroe の自動システムに統合する上で理想的な設計になっており、EZ-IO ソフトウェアを自動化に使用できます。
「2012 年初頭にハートウィグで開催されたオープンハウスイベントに出席したときに、実際に稼動する Equator と、オークマのツインスピンドルデュアルガントリー旋盤を見学しました。」と Wardell 氏は説明します。「この旋盤は我が社が製造する種類のパーツの自動化に最適なだけでなく、その Windows® ベースの OSP デュアルパスコントローラは、オープンアーキテクチャで、PC ベースのオペレーティングプラットフォームを使用していました。これらの要因は、独自の自動補正ソフトウェアの開発計画においてとても重要でした。」
自動生産セルの Equator
Wardell 氏と Buck 氏はオークマ 2SP-250H、1 台の Equator、彫刻機、FANUC M20iA 6 軸ロボットから構成されるセルを製作しました。具体的には、旋盤のデュアルパーツマガジンに、約 300 個の加工前のワークがロードされます。その後、旋盤のデュアルガントリーローダーからスピンドルにワークが送られ、完成したパーツをシュートに配置してコンベヤに送り、ロボットがパーツをピックアップします。ロボットはパーツを Equator に配置して測定を行い、合格であれば、彫刻機に転送し、最終的に完成パーツが箱詰めされ、パレットに積載されます。
「我が社では、OSP コントローラで動作する独自の工具補正ソフトウェアを開発しました。」と、Wardell は説明します。「このソフトウェアは、パーツが公差外の場合に、CSV ファイル形式で送信される Equator からの測定結果を使用して、工具をオフセットします。最も厳しい公差は 0.025 mm、表面仕上げは 0.5 ミクロンで、パーツの両側を加工して約 0.38mm を切削します。パーツのサイズは、外径 3 インチ(7.62cm)~6 インチ(15.24cm)の範囲です。「Equator を使用すると、大きなマージンで交差内の測定を簡単に行うことができます。」と Wardell は話しています。
プロセスコントロール
「半径に 5 ミクロンほどの差がありますが、正確な外径と内径を維持することができます。我が社ではサイズごとにバッチ化しているため、チャックジョーやその他の工具の交換も最低限で済みます。さらに Equator は、プロセス速度に対応できる高速性を備えています。リマスタリングは、現場を 22.2度の温度に調節しているため、一日に一度行うだけで済みます。
検査原理と自動化の柔軟性
パーツの測定方法は驚くほどシンプルです。「中央に穴を開けたアルミブロックを製作して、Equator の取り付けプレートの中央に配置しています。」と、Wardell は説明します。「これを使用して、中心を確認し、座標系を設定します。その後、各パーツをそのブロックの中心に配置し、タッチスキャンによりパーツの中心を取得し、表面スキャンによりその他すべての測定を行っています。私たちは、パーツの治具やスタイラス交換なしでも機能するように、測定プロセスを計画しました。ロボットは、Equator の EZ-IO 自動化ソフトウェアにより、パーツの種類に応じて実行する測定プログラムを選択します。私たちは、パーツが公差内であることを確認するために、重要な形状を測定する必要があることを理解しています。」
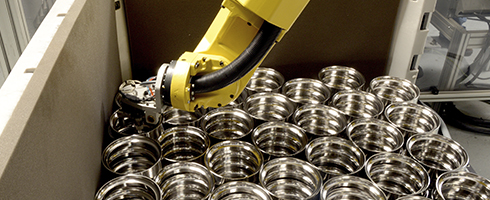
使用済みパーツの測定とソーティング
現在、ハードターニングセルでは、一日に 600 ~ 700 の完成パーツを製造しているため、以前は 2 つ必要だったセルも、現在では 1 つで済むようになっています。そのため、フォローアッププロジェクトとして、顧客用のパーツ分類セルを構想しました。現在 Wardell 氏と Buck 氏は、Touchette 氏が考案したコンセプトに基づいて、使用済みのマッドモーターのスラストベアリングレースの測定と分類を行うセルの開発に取り組んでいます。
油田整備工場では、使用したモーターを分解し、調整して、再利用します。「顧客は、パーツが再利用可能かを目視点検しています。時には、問題のないパーツを廃棄することもあり、それがコストの増加につながっていることも理解しています。」と、Wardell は説明します。「我が社では、人間による判断を排除して問題のないレースを再利用するための、簡単に組み込める測定・分類システムを顧客に提供することを望んでいました。」
この記事の執筆段階では未だに開発中ですが、Wardell 氏と Buck 氏は、2 台の Equator、FANUC LRMate 200iC 6 軸ロボット、複数レーンの低プロファイルコンベヤ、FANUC iR ビジョンシステム、ロボットのエンドエフェクター用の ATI クイックツールチェンジャーで構成されるセルを製作しています。このビジョンシステムは、どのパーツ番号が使用されているか、どの測定プログラムを実行するかを Equator に指示します。その後、問題のないパーツを適切なコンベヤに配置し、問題のあるパーツをスクラップコンベヤに配置します。
「このシステムは、ユニットとして納品し、モーター工場の人々が使いやすいようにユーザーフレンドリーに設計しているため、電源を投入してコンベヤにパーツをロードするだけで使用できます。」と、Buck 氏は説明します。
「加工セルに関しては、Equator に匹敵するコスト効果を備えた現場測定ツールは他にありません。」と Wardell 氏は付け加えています。「顧客向けのセル統合事業により、全社にとって、この分野の事業の可能性を開拓できることを願っています。」